Efficiency Without Borders: SMED's Influence Across Industries
- Ashish J. Edward
- Apr 6, 2024
- 6 min read
Updated: Oct 9, 2024
Today, we're diving into the world of Single-Minute Exchange of Die, or SMED, a groundbreaking concept developed by the legendary Shigeo Shingo. We’ll uncover how this technique can streamline processes, reduce waste, and enhance customer satisfaction across industries like healthcare, logistics, and beyond. Whether you’re dealing with automation or digitalization, SMED’s principles hold valuable lessons for optimizing the fundamentals and achieving true operational excellence. Stay tuned as we break down the six key steps of SMED and discuss how it’s more relevant than ever in today's fast-paced business landscape."
The Essence of SMED
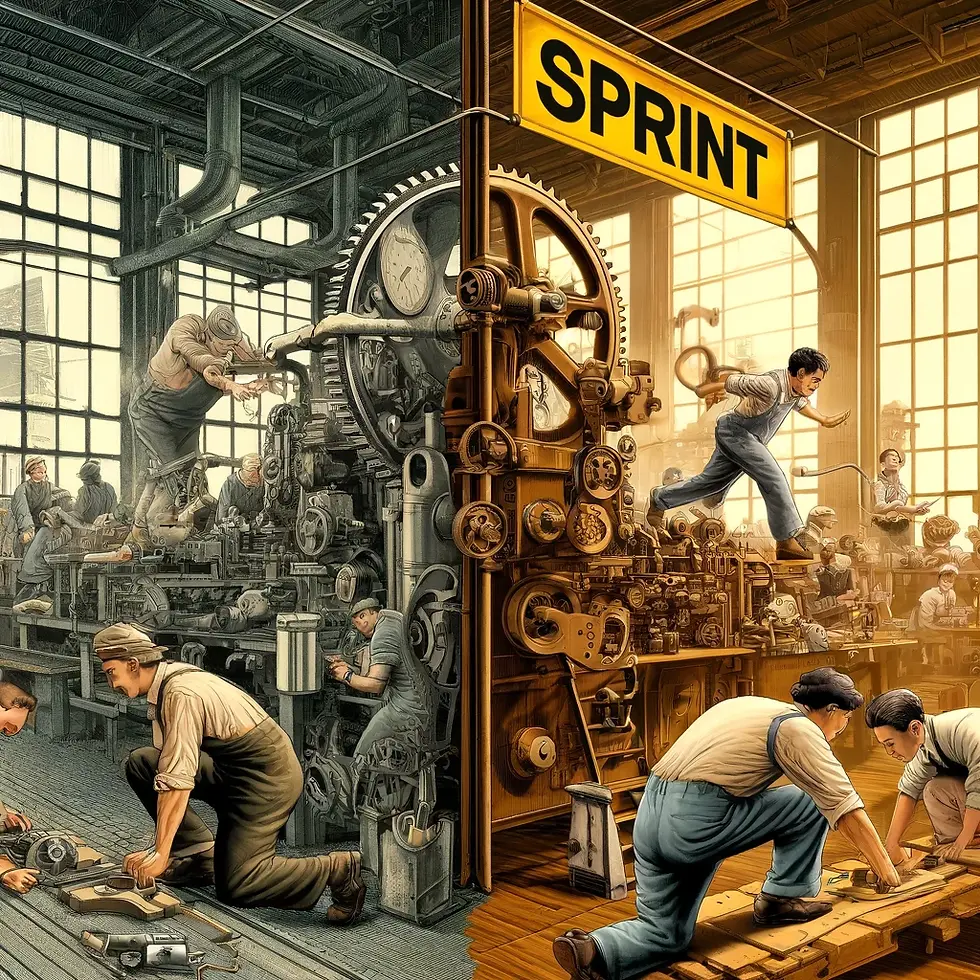
In the olden golden days, changing the setup of a machine or a production line was like planning a voyage across the seven seas - lengthy, cumbersome, and a true test of patience. Enter SMED, the brainchild of Shigeo Shingo, who looked at these marathon changeovers and thought, “Why not make this a sprint?” And thus, the concept of SMED was born, aiming to reduce equipment setup times to under 10 minutes. Yes, you heard that right. What once took hours, now mere minutes!

This vivid imagery of a Formula One pit stop serves as an engaging metaphor for SMED (most popular demonstration of the principles of SMED most of us have grown up reading and watching numerous videos :), illustrating the power of teamwork, preparation, and process optimization in achieving remarkable efficiency gains, whether on the racetrack or the factory floor. The pit crew's choreographed precision mirrors the principles of SMED in manufacturing, where the focus is on reducing machine downtime between production runs. By categorizing tasks, optimizing each movement, and ensuring that preparation is done in advance, both pit crews and manufacturing processes achieve a significant reduction in downtime, leading to increased efficiency and productivity. Pit stops have evolved from 67 seconds in the 1950s to a record 1.923 seconds, demonstrating the impact of these lean techniques. These practices ensure operational efficiency and are crucial for competitive advantage.
SMED is traditionally seen as manufacturing marvel, but it does hold the potential of making big impact in the service operations. The principles of SMED offer a remarkable framework for enhancing service delivery, ensuring that businesses can adapt swiftly to customer needs without sacrificing quality.

One notable real-world example of SMED (Single-Minute Exchange of Die) being applied outside of manufacturing, particularly in the service industry, is at FedEx Express. FedEx brilliantly applied the SMED (Single-Minute Exchange of Die) technique, traditionally used in manufacturing, to revolutionize their aircraft maintenance process during C-checks. C-checks, which are thorough inspections of aircraft, typically involve lengthy downtimes. By adopting SMED strategies amidst the 2008 recession's financial challenges, FedEx reimagined these checks to drastically cut downtime and boost efficiency.
They did this by breaking the C-check process into smaller, more manageable tasks, each within a 4-hour window, allowing the team to tackle specific areas more effectively. This smart segmentation not only sharpened the team's focus but also significantly minimized aircraft idle time.
The impact? A stunning leap in productivity at their Los Angeles International Airport (LAX) base. Before SMED, the crew managed 14 C-checks yearly. Post-SMED, this number soared to 30, cutting down the man-hours from 32,715 to 21,535. This move not only saved time but also significantly cut costs, showcasing SMED’s potent application beyond manufacturing and into the service sector.
Here’s how SMED can be a game-changer in the service sector.
At its core, SMED is about reducing the time and effort required to switch from one task to another. In service industries, this could mean anything from transitioning between customer orders in a restaurant, changing setups in a hospital ward, to varying financial services in a bank. The goal is to make these transitions as seamless as possible, minimizing downtime and enhancing customer satisfaction.

The Six Fundamental Steps Adapted for Service Industry
Observe and Document : Begin by meticulously mapping out the current processes. Understand the flow of tasks and identify where delays or inefficiencies lie.
Separate Internal from External Activities : Identify activities that must be completed while the service is not being delivered (internal) and those that can be prepared in advance or in parallel (external).
Convert Internal to External : Aim to shift as many activities as possible from internal to external without compromising the quality of service. For example, pre-setting tables in a restaurant or pre-filling forms in a consultancy firm.
Streamline All Tasks : Review both internal and external activities for optimization. This could involve retraining staff, rearranging workspaces for better flow, or implementing technology for faster service delivery.
Standardize the New Process : Once an optimal process layout is identified, standardize it across the operation. Consistency ensures that all team members can deliver exceptional service swiftly.
Implement Regular Maintenance : Ensure that all tools, technologies, and workspaces are in top condition to prevent delays. This step is about proactive maintenance rather than reactive repairs.
Adapting the Three Stages for Service Industries
Stage One - Separation of Tasks : The focus is on dissecting the service process to distinguish between tasks that can be prepared beforehand and those essential to service delivery.
Stage Two - Conversion of Tasks : involves creatively thinking about how to convert more internal tasks to external ones, thereby reducing customer waiting times.
Stage Three - Streamlining : The final stage refines all service tasks, ensuring they are performed in the least time-consuming and most effective manner.
In the service industry, the implementation of SMED goes beyond operational efficiency; it directly impacts customer satisfaction and business agility. By reducing service delivery times, businesses can respond more quickly to customer demands, increase turnover rates, and elevate the overall customer experience. Furthermore, SMED fosters a culture of continuous improvement among staff, encouraging innovation and efficiency at every level.
Lets look at an example to bring more clarity on this subject.
SMED in Action: Streamlining Emergency Department Operations
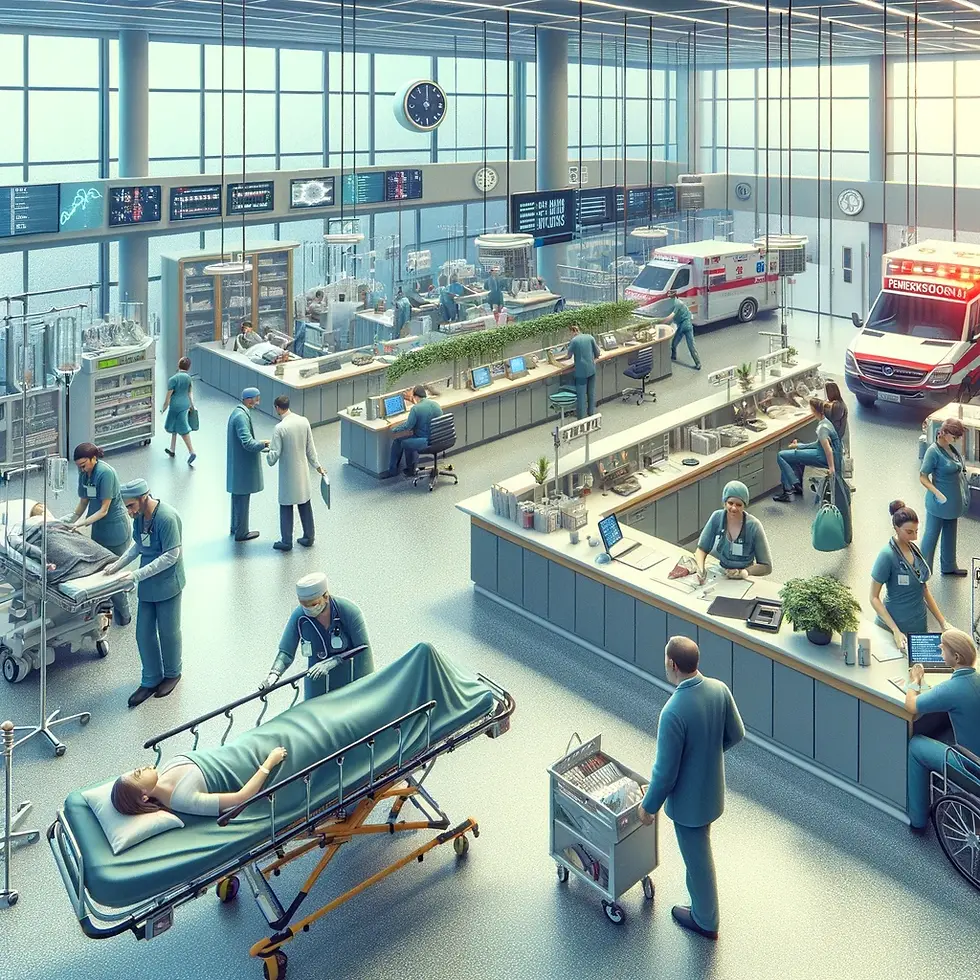
Step 1: Observing and Documenting Current Processes
The first step involved a detailed observation and documentation of all processes from patient arrival to discharge. This included patient registration, triage, medical evaluation, treatment, and discharge processes.
Step 2: Separating Internal from External Activities
Internal activities were identified as those that required the patient's presence, such as medical evaluation and treatment.External activities were those that could be prepared ahead of the patient's arrival or after their departure, such as preparing paperwork, cleaning and setting up examination rooms, or assembling medical supplies.
Step 3: Converting Internal to External
Strategies were implemented to convert internal activities into external ones wherever possible. For example, pre-triage assessments through online forms or call-ins allowed some patient data to be processed before arrival. Examination rooms were equipped and ready for various scenarios in advance, reducing the setup time for each patient.
Step 4: Streamlining All Tasks
This involved optimizing both internal and external activities for efficiency. Simplifying paperwork, using mobile data entry devices to reduce data re-entry, and reorganizing the layout of the ED to minimize movement were key steps.
Step 5: Standardizing New Processes
Once the most efficient processes were identified, they were standardized across the department. Training sessions ensured all staff were familiar with the new procedures, ensuring consistency and reliability in patient care delivery.
Step 6: Implementing Regular Maintenance
Regular maintenance of medical equipment and periodic reviews of process efficiency ensured that the setup changes remained effective and could be adjusted as needed.
The application of SMED principles here demonstrated remarkable improvements :
• Patients experienced shorter wait times from arrival to receiving care.
• The ED could serve more patients without compromising the quality of care.
• Faster, more efficient care resulted in higher patient satisfaction scores.
• Streamlined processes reduced staff stress and improved morale, as they could provide better care without unnecessary delays.
This real-world application of SMED in the healthcare sector underscores its versatility beyond manufacturing. By focusing on reducing setup times (in this case, the time to prepare for and deliver care), hospitals can significantly enhance service delivery, demonstrating SMED's potential to foster efficiency and improve outcomes in service industries.
In conclusion, the timeless ingenuity of SMED transcends the factory floor, infiltrating every facet of our lives with its call for efficiency. In a world increasingly dominated by digital processes and automation, SMED reminds us that the quest for optimization is not just about advanced algorithms or cutting-edge technologies. It's about reimagining the fundamentals—streamlining our processes, reducing our waste, and, most importantly, saving our most precious commodity: time. As we continue to push the boundaries of what's possible with AI and data science, let's not forget the basic principles like SMED that teach us the art of doing more with less. After all, in the pursuit of future innovations, it might just be these timeless concepts that hold the key to unlocking our full potential and propelling us towards a more efficient, productive future. Who knew that Shigeo Shingo’s sprint philosophy would set the pace in a race where robots and algorithms are our teammates?
Comments